Silicon Carbide Grinding Wheel Dresser
CRATEX rubber-bonded silicon carbide dressing stick for grinding wheels is ideal tool for truing, dressing and shaping different types of grinding wheels including CRATEX rubberized abrasive wheels. It is a perfect solution to keep your grinding wheel flat, sharp, clean and running smoothly!
With this easy to use, efficient and long-lasting dresser you'll enhance your grinding wheel cutting and finishing performances. It's simply a MUST for everyone who continuously uses a bench grinder.
Use CRATEX cleaning abrasive sticks and minimal effort and your grinding wheel will be in a top-notch form in just a few minutes. Simply choose the dressing wheel shape, grit and length and before you know it, your order will be on the way!
Recommended for CRATEX Large Grinding Wheels : Dressing Stick Size: 6” x 1/2” x 1/2”
Click the icon to jump to the desired section
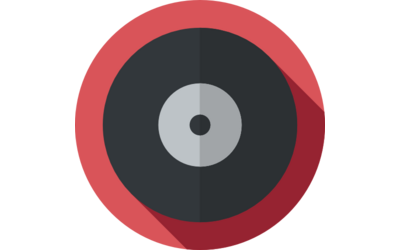
CHAPTER 1
What is Grinding Wheels Dressing
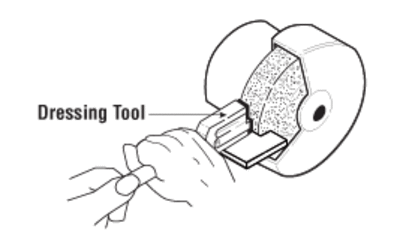
CHAPTER 2
Grinding Wheel Dresser
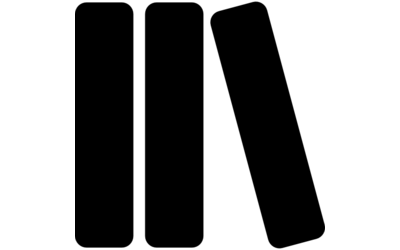
CHAPTER 3
CRATEX Dressing Stick
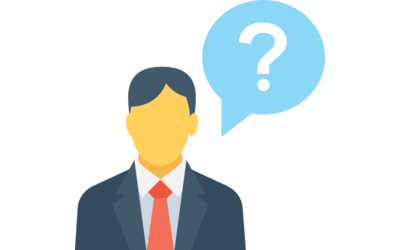
CHAPTER 4
What Is The Difference Between Dressing And Truing?
What is dressing
CHAPTER 1
Grinding wheels are tools used most often for grinding (abrasive cutting) operations. In our article dedicated to grinding wheels we already explained that grinding wheels are designed as self-sharpening tools, which means that the grinding process itself sharpens the wheel every time it’s used. Small abrasive cutting grains of the wheel become dull during the grinding process and break away from the bonding material, leaving the sharp grains exposed. However, this awesome self-sharpening ability is not quite enough, since the work material can cause it to load up, so it is necessary to occasionally dress or true the wheel to achieve satisfying results. If the wheels are not maintained, increased cutting forces and the created heat can cause damage to the surface finish and wheel breakage. Dressing is not so much important for rough grinding wheels, but you’ll need to always have a true, flat face on your wheel in case you’re doing some precision grinding.
Here’s where the grinding wheel dresser steps in. It is a handy tool used to remove the top layer of a grinding wheel in the purpose of:
- Truing it and making it concentric, which will minimize vibrations and improve the quality of the finishing operations. Loaded or clogged areas on the wheel will cause it to lose its roundness, and the loss of the roundness will eventually cause excessive vibrations of the bench grinder. The reason why the wheel loses its shape is because the clogged areas wear off at a different rate from the less loaded areas;
- Exposing fresh abrasive grains, which will enhance the cutting action. Dull grains of the wheels with extremely hard bond will usually remain in the wheel;
- Cleaning the pores between the abrasive grains, which get filled with workpiece fragments. This happens in case the workpiece has a softer grade than the one the wheel is designed for. In that case, the grains won’t break away in time and the workpiece parts will get stuck between them.
With dressing, the wheel will be good as new and ready for renewed grinding action!
Grinding Wheel Dresser
CHAPTER 2
Grinding wheel dressers can be broadly divided in following categories:
- Dressing rolls and rotary tools – these dressers have rolls or wheels that are coated with diamonds;
- Dressing spindles - spindle-mounted tools that usually come with an integral brake and drive;
- Dressing sticks – or dressing blocks are made of bonded abrasives;
- Impregnated or grit dressing tools – these have a whole layer of diamond or superabrasive grains bonded in the matrix, much more sharp points than an ordinary multi-point tool. These are used in the same way as multi-points tools, but they are designed to provide a superior finish;
- Single-point dressing tools – these have only one diamond or superabrasive grit bonded in the tip and can be various: single point tools should be mounted at a 10°-15° angle to the wheel centerline while the contact point should be slightly below the centerline. The tools should point in the direction of wheel travel;
- Multi-point or Cluster dressing tools – unlike the single-point ones, cluster dressers have several diamonds or superabrasives across the dresser surface. They can be wide enough to reach across the entire cutting surface of the grinding wheel and most of them are used for straight-face dressing. They came into use mostly because they’re more affordable (instead of one large diamond they have several smaller ones).
Grinding wheel dressers used most often on bench grinders are as follows:
- Dressing sticks
These are dressing bonded abrasives shaped as a stick or a block. You’ll usually use dressing blocks made from the same abrasive type as the grinding wheel, but you’ll choose a stronger bonding agent. Typical abrasives used in grinding wheel dressing sticks are aluminum oxide and silicon carbide. For resin and vitrified bond diamond and cBN wheels you should choose a dressing stick that is one or two grit sizes finer than the abrasive in the wheel. For metal bond diamond choose a stick the same grit size or one grit size coarser than the wheel abrasive.
- Star or disc dressers
These are heavy-duty dressers with long handles, a row of hardened free running either star-shaped cutters or wavy discs, and little ‘legs’ that are designed to go behind the tool rest. Star dressers provide a more ‘open’ texture, which is perfect for rough grinding, and they are more suitable for larger (e.g. 12″) grinders. They are consumable items that are going to wear down, so you’ll need to change the discs after they do.
- Diamond Dressers
These dressers have a short handle and you can find two types. Either those with a single diamond embedded in their face, or those with a lot of small diamonds embedded in a wide surface. Diamond is the hardest superabrasive used for truing and dressing conventional and superabrasive grinding wheels. It’s ideal for fine finishing cutting tools as it gives the grinding wheel a smoother finish. Although diamond dressers might seem pricey initially, rest assured you’ll get your money’s worth, since diamond is extremely durable and therefore a long-lasting tool.
When it comes to CNC grinders, four types of dressers can be used for dressing their wheels.
- Crush rolls
This is a wheel made of either high-speed steel or tungsten carbide, which is pressed against the grinding wheel while spinning at the same speed as the wheel. The dresser profile is the mirror image of the desired grinding wheel profile and cannot be adjusted, only replaced by a different profile.
- Diamond crush rolls
This would be a crush roll which is coated with diamond grains. Diamond grains give them an advantage over regular crush rolls, because they wear more slowly.
- Stationary dressers
These have a metal blade that has a single diamond embedded in the tip. A CNC program for dressing the wheel controls the wheel’s profile and is responsible for moving the dresser across the wheel’s surface.
- Rotary dressers
These are sometimes called ‘pizza cutters’. A disc made of material (usually a diamond) is attached to the edge, and the grinding wheel’s profile is controlled by the CNC program used to wheel dressing as well.
CRATEX Dressing Stick
CHAPTER 3
CRATEX silicon carbide grinding wheel dresser dresser is a perfect tool for dressing and truingdifferent kinds of grinding wheels including all rubber-bonded abrasive wheels. Thanks to its shape, fast cutting abrasive with a hardened bond, it’s an efficient, easy to handle and a long-lasting dressing stick that will help you achieve maximum performance from all your CRATEX rubberized abrasive wheels.
Selecting the appropriate dressing stick will depend on the size, type, speed, grit size and specification of the wheel, and of course, the workpiece material. A good advice would be to test several sticks to find the best possible solution for your needs.
RECOMMENDED: Check out CRATEX Mini Test Block Kit No.128B (shipping and handling included in the price)
Dressing sticks are used for dressing and truing bench and pedestal grinder wheels. You’ll only need your hand and a dressing stick to perform the dressing which is done by moving the stick back and forth against the wheel face. In case the movement is fast, so will be the metal removal, which will cause rougher finishes on the workpiece. If the movement is slower, the grinding wheel face will be smoother, there will be less metal removal and the surface finish on the workpiece will be finer.
CRATEX dressing sticks are a perfect solution to keep your grinding wheel flat, sharp, clean and running smoothly! A MUST for everyone who continuously uses a bench grinder!
What Is The Difference Between Dressing And Truing?
CHAPTER 4
Both dressing and truing must be conducted in the purpose of creating satisfactory work. Both operations remove material from the grinding wheel. While dressing relates to a surface finish maintenance, truing relates to the loss of form control due to the excessive edge wear.
Although sometimes together referred to as ‘conditioning’, they mean two different operations. Conventional grinding wheels that are inexpensive can be trued and dressed at the same time and the process can be repeated periodically. However, superabrasive grinding wheels, like CBN or diamond wheels, are a serious investment and require much more attention to dressing and truing separately.
Truing is done when a new wheel is installed and before it’s used for the first time and is necessary for precision grinding. The purpose of truing is to bring every point of the grinding surface concentric with the machine spindle (to establish concentricity) and to introduce a form (shape) into a wheel. No matter how precisely manufactured, there will be a slight gap between the wheel bore and the machine spindle. Even if the gap is one thousand of a millimeter, problems like chatter marks will occur if the wheel is not trued to the center of the spindle. Conventional grinding wheels can be trued easily with a diamond cutter that is harder than the wheel, while the superabrasives cannot be cut and must be ground to size. This is done by using a sintered diamond roller or by traversing a conventional grinding wheel. Many like to use a brake-controlled truing device called BCTD which turns more slowly and provides a more precise and controllable truing. After the truing process, the wheel surface is smooth and closed, and since there are no abrasive grits exposed, the wheel can’t perform cutting.
Dressing is the process that comes after truing (especially in the case of superabrasives) and it represents grinding wheel sharpening by exposing abrasive grits above the bond. In other words, removing small chips of workpiece lodged in the wheel surface or removing dull abrasives which returns the wheel to its original dimensions and provides crystal exposure. The wheel surface after dressing is open with grits exposed.